Depuis 3 ans, Englab, intégrateur strasbourgeois, développe une ligne de production expérimentale. Sa vocation ? Améliorer les performances organisationnelles et décisionnelles des outils de production. Comment ? En testant, mesurant et analysant la validité des briques technologiques qu’ils développent. Tous les outils et principes directeurs de l’industrie 5.0 sont largement utilisés pour la flexibiliser et digitaliser la ligne. Et c’est notamment auprès de SICK que les ingénieurs d’Englab ont trouvé la plupart de leurs capteurs d’automatisation.
Une ligne de production 5.0 expérimentale développée par Englab et boostée par SICK
ENGLAB : L’Innovation au service de l’Industrie du Futur
ENGLAB est un bureau d’études mécatronique et intégrateur industriel, situé à Schiltigheim. Il offre des solutions personnalisées pour externaliser le développement de produits normés et de processus industriels. Sa mission : être le partenaire unique du développement complet des produits de ses clients.
Ses trois piliers sont :
- SMART PRODUCT : Conception et développement de produits mécatroniques.
- SMART VALIDATION : Systèmes de test et validation sur-mesure.
- SMART INDUSTRY : Automatisation et conception de lignes de production innovantes.
Avec une approche de fertilisation croisée des technologies, ENGLAB propose des solutions clés en main. Réalisant 8 M€ de CA, l’entreprise compte quatre équipes d’études (dont 1 axée R&D&I) et un atelier industriel de plus de 1 000 m² pour prototyper,tester, et produire.
Projet Industry x.0 : une réponse aux enjeux de réindustrialisation
Début 2020, pour répondre aux problématiques de réindustrialisation et à la customisation des produits, ENGLAB se lance sur l’intégration in situ des briques R&D à travers une plateforme expérimentale 5.0. Les enjeux de réindustrialisation de la France sont importants. Les outils de l’Industrie 4.0 et 5.0 offrent des perspectives de compétitivité intéressantes (coûts de production compatibles avec les marchés visés) et une flexibilité de production jusque-là complexe à atteindre. L’expérience d’ENGLAB multisectorielle et la connaissance des problématiques métier des industriels, est un atout de taille. Avec l’accompagnement de la Région Grand Est, le projet Industry x.0 est né.
L’objectif est de déployer et de tester différentes briques technologiques (automatisme, IIoT, cobotique, réalité virtuelle et augmentée, Intelligence Artificielle, système de tests intelligents…), d’analyser la facilité de déploiement , et l’impact en matière de performance organisationnelles (processus) / décisionnelles (prendre la bonne décision rapidement). La qualification des opérateurs, la prise en compte de handicaps, la formation sont aussi des aspects étudiés.
Postes de la Ligne de Production Expérimentale
Pour répondre aux problématiques techniques et scientifiques, l'organisation de la plateforme a été conçue de manière à être représentative des processus industriels classiques. La ligne est donc constituée de :
- un poste d'approvisionnement digitalisé
- un poste d'assemblage des produits assisté par IA
- un poste de test et validation modulaire
- un poste de contrôle qualité assisté par IA
- un poste de conditionnement assurant la traçabilité et la qualité du produit en sortie de production
- un système de convoyage des produits conditionnés flexible et automatisé
Face aux enjeux d'automatisation, de digitalisation, de robotisation, d'environnement et de collaboration avec l'humain, la ligne est composée d'une armoire principale disposants des fonctions principales (automates, pilotages et contrôle électrique, IHM, safety, …). La ligne se veut flexible et modulaire avec une possibilité d’interchangeabilité des postes pour répondre à une éventuelle évolution de produits ou d’un changement de process.
Chaque poste dispose d’automates déportés pour répondre à ces fonctions de flexibilité. Pour plus d'agilité et de securité, un cobot permet de transférer les produits entre les stations.
Flexibilité et Performance : Les clés de l’Industrie du futur
Pour valider l'agilité et la flexibilité du process et des briques technologiques développées, la ligne fonctionne pour trois produits complètements différents. Sur cette plateforme sont produits des flacons, des porte-clés électroniques ainsi que des tablettes tactiles. Cette diversification permet d'élargir les expérimentations tant sur le process global que sur les prises de décisions des opérateurs.
Si l’objectif de cette plateforme est d’étudier les avantages permettant d’augmenter les processus organisationnels et décisionnels, ce sont l’ensemble des nouveaux piliers de l’industrie 5.0 qui seront étudiés :
- Soutenir l’humain
- Gestion de l’équilibre entre efficacité et productivité
- Tirer le meilleur parti des nouvelles technologies
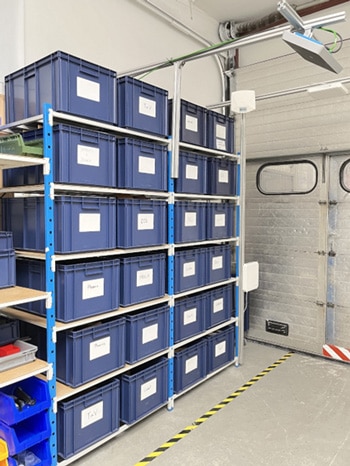
Sur le poste d’approvisionnement digitalisé, un RFU65x a été déployé. Il lit les bacs et leur contenu en simultané. On sait donc ce qui est en stock et quelles pièces sont parties en production. Une station d’identification permet aussi de coder les tags RFID posé sur les flacons, pour les suivre pendant la production.
Le poste d’assemblage propose un niveau d’assistance réglable, en fonction de la complexité et du niveau de connaissance de l’opérateur. L’IA intégrée rend le poste adaptable, même pour les personnes avec handicap et apprend au fur et à mesure. Ce poste intègre un RFU61x pour la traçabilité et une caméra PLOC2D pour aider le robot à prendre le produit pour l’amener au poste suivant.
Ce poste de test et de validation est totalement modulable. En amont, un RFU61x fait le suivi de traçabilité (vérification du bon produit pour la bonne tâche) puis un robot vient faire différents tests fonctionnels et électriques du produit. . Un scrutateur laser de sécurité S300 Mini protège une zone d’accès pendant l’opération.
Au niveau du poste de conditionnement, la mise en carton et l’étiquetage s’opèrent. Une fois conditionné, le carton glisse sur un convoyeur où une caméra de lecture de code Lector63x recueille les informations de traçabilité indiquée dans le code QR (lot, type de produit, date, opérateur, poids, destination, rayonnage). Le carton est ensuite poussé dans le bon bac selon le type de lot. Cette action est possible grâce au RFU61x qui identifie le lot et son contenu. Le convoyeur est équipé de différents systèmes SICK : FTMg et PAC50 pour l’approvisionnement d’air comprimé et le contrôle de fuite des vérins poussoirs qui mettent le carton dans le bon bac. Un MBP10 mesure les vibrations du moteur et 3 autres mesures les vibrations, chocs et température au niveau du cobot et de l’axe linéaire. Une passerelle SIG350 et un TDC complètent l’ensemble pour pouvoir collecter l’ensemble des données de ces capteurs. Celles-ci sont remontées dans un tableau de bord pour détecter toute anomalie de production, à distance, et sans avoir besoin de s’interfacer avec l’automate.
Un accompagnement tourné vers les dernières nouveautés
Hormis quelques points de blocage de développement, rapidement surmontés, le projet s’est déroulé sans encombre.
Selon Vivien Schmitt, responsable du projet : « l’instrumentation en place est robuste, elle remplit toutes les spécifications fixées. Elle offre de la flexibilité, indispensable pour ce projet ». Accompagné de Sylvain Kaufman, ingénieur commercial SICK, toutes les nouveautés SICK sont systématiquement proposées, car « intégrer des nouveaux produits sur une ligne expérimentale démontre la validité de la solution et permet également aux clients de tester la solution sur des situations réelles de production » poursuit Vivien Schmitt.
Par ailleurs, la revente de briques technologiques telles que développées les rend bien plus accessibles. « Avec l’expérience et le temps de développement gagné, ces solutions reviennent aussi moins chères pour le client final » conclu Antony Funaro, responsable commercial d’Englab.
Et demain ?
La plateforme poursuit ses développements. La géolocalisation Indoor (et Outdoorr) sont les nouvelles pistes d’exploration. Pour cela, la solution Tag Loc équipe désormais le démonstrateur, afin de suivre les déplacements du robot mobile autonome en fin de ligne. La perte de produits, de matériels, de palettes est très fréquente chez les clients. La logistique au sein même de la production est un secteur à fort potentiel. Les enjeux des industriels sont de mieux gérer les flux entrants et sortants.
ENGLAB se positionne comme un acteur clé dans la réindustrialisation française, en proposant des solutions technologiques de pointe adaptées aux besoins croissants de l'industrie. SICK partage cette mission et est fier de les accompagner sur ce chemin.
Ces articles pourraient vous intéresser
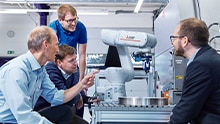
Détermination de la position en 2D avec un système de guidage du robot

Géolocalisation indoor, des solutions pour une efficacité intralogistique maximale
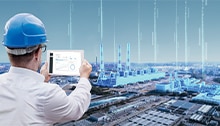
Intégration des données de production : la proposition de SICK