Flexibilization is currently a hot topic in every manufacturing company. The people at TechNikkels already recognized this some time ago. Thanks to their longstanding experience in packaging for a wide variety of industries, the company from Holten in the Netherlands offers a complete range of packaging solutions for different kinds of boxes, cups, buckets, canisters, and bottles. SICK is their preferred partner and adviser for all sensor solutions.
Boxes, cups or bottles: flexible packing of the highest standard
TechNikkels was established in 2002 as an engineering firm. Thijs Krijgsman, Manager Sales & Services, reports: “The current director, Henk Nikkels, had been visiting companies in all possible industries for many years to discuss various packaging issues. Time and time again he observed that his customers had sealing and filling machines standing around that could only be used for a limited number of bottles or seals. When the customer wanted to use a different bottle or a different seal, the machine could no longer be used. Henk succeeded time and again to modify the existing machines in such a way that the customer could continue to use them in production.”
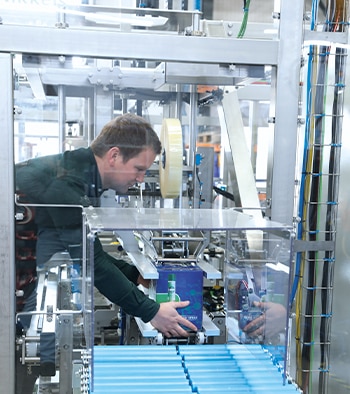
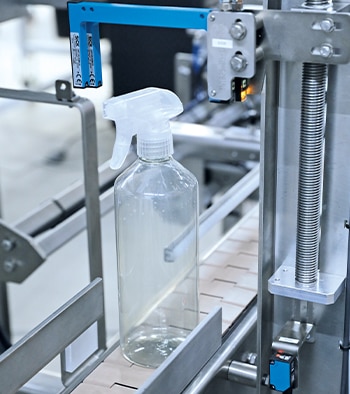
Since 2015, TechNikkels has been intensively working on developments such as Remote Support. According to Thijs Krijgsman, Manager Sales & Service: “We can take a look at the customer’s machines at anytime remotely – where are the error messages coming from? What process is not running properly? We can often achieve a lot with a few remote instructions. Contacting us should be as simple as possible. When customers have a problem, we want to help them quickly. Despite the rapid growth of our company, we endeavor to continue to uphold our service standards.”
Nearness to the customer
Another contributor to the company’s high standard of service is the industrial image processing solutions that are integrated into almost every TechNickels product. Krijgsman presents an example image: “We can actually see here what is happening on-site in the machine. On this timeline you can see exactly when a problem arose. Then I open the captured image and see that this seal is not seated correctly on the bottle.”
How do customers view the cameras from a data privacy perspective? “Every customer is free, of course, to choose not to use the cameras. In any case, we work via a VPN connection that does not lead to the company's network but instead runs over the router. In some cases, customers have also set up their own security measures, such as their own VPN or a firewall. Most customers these days have recognized the great benefit of the cameras,” says Krijgsman.
Condition monitoring and monitoring of the overall equipment effectiveness (OEE) have also gained importance at TechNikkels. Large quantities of data about the machine are collated into useful information on OEE dashboards. These make all processes highly transparent for the customer. According to Thijs Krijgsman: “If, for example, the availability suddenly drops to around 60 %, we very quickly receive a notification. This enables us to sometimes act before the customer even notices anything. And that’s how we are further developing our strategy of ‘Nearness to the customer’.”
Is the cap seated correctly on the bottle?
SICK is contributing to TechNikkels’s success with a variety of sensor solutions. According to Thijs Krijgsman: “The blue color tone of SICK can be seen almost everywhere. In this filling and sealing machine, for example, we use a fork sensor that detects whether the seal is seated too high on the bottle or even missing completely. Defective bottles are separated out. Here you can see another vision sensor in the Inspector series. The relevant unit is used to align the bottles. The vision camera then checks whether the bottle is standing in the correct position and in the correct orientation or needs to be rotated.
Ongoing inspiration and always a solution on hand
TechNikkels and Thijs Krijgsman purposefully chose SICK: “We stand for high-quality machines and therefore also seek to purchase components of high quality. Furthermore, SICK, just like us, is very service-oriented. Their regional manager visits us often and helps us tremendously with any questions relating to our quotations. He always has a solution on hand. We are continuously further developing our product portfolio. It’s great that SICK inspires us in this regard, for example with our IO-Link solutions.”