Thanks to their consistently modular machine concept, the top-loading machines produced by Schubert in Crailsheim, Germany, are among the most flexible solutions of their type. Despite the functions are so versatile, Schubert is able to solve 90% of all detection tasks with just three of SICKs sensor ranges, including the specially for Schubert modified WTB12-3 proximity sensor with integrated self-monitoring. Top-loading machine. Photo: Gerhard Schubert GmbH.
For anyone wishing to package products and product ranges by the piece with high precision and economic efficiency, there is no way around the TLM (top loading machines) solutions of Gerhard Schubert GmbH. Whether one deals with a packaging machine, picker line, packaging line, or thermoforming equipment - the TLM machine design developed by Schubert manages with only seven basic subassemblies. This consistent modularity allows technically and economically efficient, all-in-one solutions for the most diverse packaging applications.
A WTB12-3 photoelectric proximity sensor with background suppression which has been specially modified for Schubert is used in the lions share of applications. With its specific optical and evaluation properties and self-monitoring to protect against tampering, this sensor is a dominant force in our modular machine concept, confirms Siegfried Rottler, Group Head of Control Technology at Schubert.
On the way to the ideal solution for Schubert
One of the many applications is the monitoring of the magazine in top-loading erectors. The WTB12-3 is used for cutting and fill level monitoring; the sensor also triggers the emergency stop function when the machine is empty. Integrated background suppression makes the WTB12-3 particularly suitable for use in packaging machines. It also impresses with how easy it is to mount and operate. Even better, its rugged metal housing is resistant to cleaning agents. For us, it wasnt only sensor performance and compatibility for integration that were crucial where the photoelectric proximity sensor was concerned. It was the fact that the entire W12-3 product family is a platform on which we can have at our disposal all optical principles in a single housing concept that is flexible in terms of its design and build, continues Siegfried Rottler. In addition, SICK has a proven track record of providing sensors to meet our specific requirements quickly, so that the devices can be tested shortly afterwards and converted into special version products within reasonable lead times.
Modification on the basis of a proven product platform
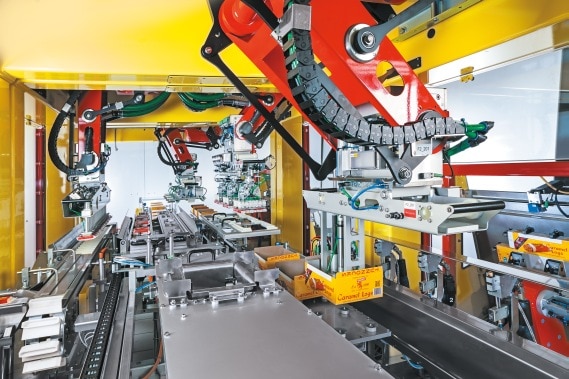
Top-loading machine. Photo: Gerhard Schubert GmbH
When swung in, the buffer magazines almost serve as barriers blocking access to the erector tools and drives inside the machine. To ensure that the sensors could not be tampered with or bypassed and to maintain access to the interior of the machine when a magazine is open, Schubert requested the integration of self-monitoring function and object surveillance. The special ASIC technology developed by SICK and also used in the WTB12-3 makes this possible with an oscillating output. A feeder circuit integrating the sender LED, the object to be scanned, the receiver, and the electronics, oscillates at approx. 10 Hz. This enables the presence of the blanks magazine to be scanned for continuously, virtually excluding the risk of tampering altogether. Also, at the specific request of Schubert, the photoelectric proximity sensor has been factory-set to a fixed scanning range of up to 300 mm. This speeds up the configuration process during machine integration.
Reliable detection and quick alignment thanks to light-intensive PinPoint-LED
Thanks to the clearly visible light spot of the light-intensive PinPoint sender LED on the cartons, the WTB12-3 can be aligned quickly and easily. During operation, the detection response is very stable and reliable. The sensor is suitable for all conceivable surface designs, says Siegfried Rottler.It doesnt matter if the machine is working with black or white surface finishes or even cartons with shiny custom print finishes. Even mechanical integration can be achieved with ease, as the housing dimensions, hole pattern, and mounting bracket of the custom version match those of the entire standard product family 1:1.
Complex requirements as an incentive for improvements
Schubert has been using the W12-3 product family as a sensor platform for many years. Its appearance in countless of the companys applications has led to much experience being gathered of the various sensors. This has resulted, for example, in the sensor technology of even the specially designed WTB12-3 photoelectric proximity sensor being modified to give all types of packaging machine an additional benefit, whether as an innovative sensor solution or providing the basis for better design. Whats crucial is that SICK speaks our language, is able to integrate and convert requirements from the packaging sector, and is so quick and flexible in everything it does, summarizes Siegfried Rottler.
Reliable in series: WTB12-3 in use at Schubert
- Product information: WTB12-3 photoelectric proximity sensor
- Product portfolio: Photoelectric sensors
- More information: Gerhard Schubert GmbH